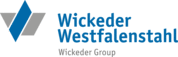
Catalog excerpts
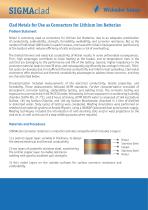
SIGMAclad Clad Metals for Use as Connectors for Lithium Ion Batteries Problem Statement Nickel is commonly used as connectors for Lithium Ion Batteries, due to an adequate combination of conductivity, solderability, strength, formability, weldability, and corrosion resistance. But as the number of individual 18650 cells in a pack increase, one issue with nickel is heat generation (particularly at the busbar) which reduces efficiency of cells and poses a risk of overheating. The limited thermal and electrical conductivity of Nickel results in some unfavorable consequences. First, high amperages contribute to Joule heating at the busbar, and to temperature rises in the cell that are damaging to the performance and life of the battery. Second, higher impedance in the connector material leads to more IR drop, and consequently significantly less voltage in the cell. Third, hot spots can develop due to insufficient thermal conductivity and inferior heat spreading. Clad metal connectors offer electrical and thermal conductivity advantages to address these concerns, and they are characterized below. Characterization included measurements of the electrical conductivity, tensile properties, and formability. These measurements followed ASTM standards. Further characterization consisted of atmospheric corrosion testing, solderability testing, and welding trials. The corrosion testing was exposure to a corrosive dip in ASTM 2570 water, followed by 16 hours exposure in a condensing humidity chamber (100% RH, 37.7oC), and 8 hours of drying. ASTM D2570 water is composed of 148 mg Sodium Sulfate, 165 mg Sodium Chloride, and 138 mg Sodium Bicarbonate; dissolved in 1 liter of distilled or deionized water. Sixty cycles of testing were completed. Welding simulations were performed on selected clad material systems at Amada Miyachi, using a 300ADP (advanced dual pulse) power supply. Welding techniques included the introduction of anti-shunting slots and/or weld projections to the clad strip, as well as the use of a step-welding process when required. Materials and Procedures SIGMAclad connector material is a metallic laminate composite which includes 5 layers: 1) a central copper layer, variable in thickness, to design the desired electrical and thermal conductivity 2) two layers of austenitic stainless steel, sandwiching the central copper layer, to enable resistance welding with good to excellent pull strengths Nickel Stainless Steel Copper Stainless Steel Nickel 3) thin nickel layers on the outside surfaces for surface corrosion resistance and solderability.
Open the catalog to page 1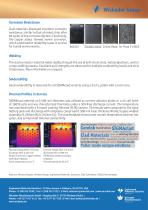
Corrosion Resistance Clad materials displayed excellent corrosion resistance, similar to that of nickel strip, after 60 cycles of the corrosive dip test. Conversely, the copper alloys showed severe corrosion, which could lead to reliability issues in service for humid environments. N02201 Welding The clad connector material welds readily through the use of anti-shunt slots, weld projections, and/or a step welding process. Excellent pull strengths are observed for multiple conductivity levels and strip thicknesses. More information on request. Solderability Good solderability is observed for...
Open the catalog to page 2All Wickeder Westfalenstahl GmbH catalogs and technical brochures
-
SIGMAclad 60
1 Pages
-
Innnovative Clad Designs
2 Pages
-
Clad Materials
8 Pages
-
CopperPlus
3 Pages