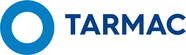

Catalog excerpts
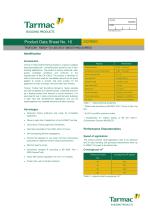
Product Data Sheet No. 16 TRUFLOW - READY-TO-USE SELF SMOOTHING SCREED Identification Introduction Property Tarmac Truflow Self Smoothing Screed is a calcium sulphate based pumpable self – smoothing floor screed for use in floor levelling applications. The product is factory produced under quality controlled conditions and conforms to the requirements of BS EN 13813. The product is delivered to site by truck mixer ready for immediate use and can be pump applied to create a smooth and level surface for the application of floor coverings, tiles and other floor finishes. Compacted, set and air dried density Flexural strength class Flow properties Drying shrinkage Open to foot traffic Tarmac Truflow Self Smoothing Screed is highly versatile and can be applied as a bonded screed, unbonded screed or as a floating screed over thermal or sound insulation. It is also ideal for use in most commercial and domestic buildings in both new and refurbishment applications and can be readily applied over installed electrical and other services. Setting time Thermal Expansion Thermal Conductivity Fire rating Table 1 – Typical physical properties 1 Delivered factory produced and ready for immediate application. Allows a rapid rate of application of up to 2000m 2 per day. Determined according to BS 8204: Part 7 annex A flow ring test. 2 Classification A1 without testing to BS EN 13501-1 (Commission Directive 96/603/EC). Laid only by Tarmac approved Contractors. Normally accessible to foot traffic within 24 hours. Self-compacting without segregations. Permits the designer to use lower minimum thicknesses compared to traditional cement sand screed systems Minimal need for joints. Soundness category A according to BS 8204: Part 1 (BRE Screed Test) Class SR2 surface regularity (≤ 5 mm in 3 m length). Protein free, will not harbour bacteria. Performance Characteristics Speed of application This product permits rapid application rates to be achieved and its easy handling and pumping characteristics allow up to 2000m2 of screed to be laid per day. Coverage Area M2 (approx) Table 2 – Approximated coverage per m
Open the catalog to page 1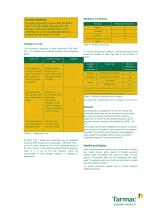
Minimum Thickness Surface regularity A surface regularity of class SR2 BS 8204: Part 7 can be readily achieved with this product. That is the departure from the underside of a 3 m straightedge resting in contact with the floor is ≤ 5 mm. Floor type Over conduits and over heating Table 4 – Minimum thickness The soundness categories of floors described in BS 8204: Part 1 for bonded and unbonded screeds are summarised below: Type of use For all floor types abrupt changes in screed thickness should always be avoided as these may lead to the formation of cracks. screed Areas expected to Hospital...
Open the catalog to page 2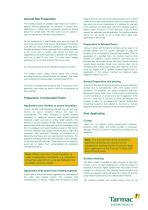
General Site Preparation The building should be weather tight before the screed is applied. Where appropriate, for example in ground floor applications, a damp proof membrane should be placed below the screed base. The floor area must be swept or vacuum cleaned and free from any projections. For all applications a foam border strip must be fixed all around the perimeter of the area to be screeded. The border must also be fixed around any upstands. If adjoining areas through doorways or other openings are not being screeded at the same time, a border strip should be fitted and supported...
Open the catalog to page 3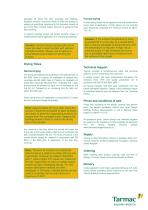
adequate for some thin floor coverings and coatings, therefore provision should be made to finish the screed by applying a smoothing compound to the hardened screed as part of the floor covering system just prior to laying the final floor covering. Forced drying Forced drying should not be applied to the final screed within seven days of application. Further advice can be provided upon request by contacting the Technical Centre on 08701 116 116. A Calcium sulphate screed will almost certainly require a suitable primer before application of a smoothing compound. Caution: Cement based...
Open the catalog to page 4
REFERENCES British Standards Institute BS EN 13454 Binders, composite binders and factory made mixtures for floor screeds based on calcium sulfate. Mixing water for concrete – specification for sampling, testing and assessing the suitability of water, including water recovered from processes in the concrete industry, as mixing water for concrete Code of Practice for installation of sheet and tile flooring. Code of Practise for the installation of textile floor coverings. Screeds bases and in situ floorings. Part 7: 2003 Pumpable self-smoothing screed – Code of Practice Screeds bases and in...
Open the catalog to page 5All Tarmac Building Products catalogs and technical brochures
-
Topcrete
15 Pages
-
Hemelite
15 Pages
-
Durox
17 Pages
-
Toplite
14 Pages
-
Coloured Mortar Brochure
6 Pages
-
Topblock Sitework Guide
28 Pages
-
Topblock design guide
56 Pages
-
Hemelite and Topcrete
28 Pages
-
Toplite aircrete blocks
16 Pages
-
Durox aircrete blocks
32 Pages
-
Thin joint blockwork
31 Pages
Archived catalogs
-
Tarmac Building
12 Pages