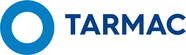

Catalog excerpts
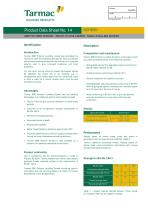
Product Data Sheet No. 14 SBR POLYMER SCREED - READY-TO-USE CEMENT: SAND LEVELLING SCREED Tarmac SBR Polymer Levelling screed was developed by Tarmac to meet the increasing demand for factory produced cement sand levelling screed with the inclusion of a synthetic polymer resin to give increased toughness and bond properties. Tarmac SBR Polymer Levelling Screed is a thoroughly mixed, accurately controlled blends of the following materials: For new work, normal minimum screed thinknesses should be specified, but where this is not possible, e.g. in refurbishment work, where levels must be maintained, there is often a need for a thinner screed which must be well bonded to the base. Well-graded washed fine aggregate (sand) conforming to BS EN 12620 / BS EN 13139 Portland Cement conforming to BS EN 197-1 Styrene butadiene resin polymer emulsion. Retarding/water reducing admixture conforming to BS EN 934-2/3 giving the optimum working time, normally usable for 8-12 hours from the time of mixing Water conforming to BS EN 1008, to give the optimum semi-dry consistency for easy laying and thorough compaction Advantages Tarmac SBR Polymer Levelling Screed has the following advantages over traditional cement sand levelling screeds: Factory mixed to give accurate dispersion of cement and polymer. Conforms to the compressive strength requirements of BS EN 13813. Minimises shrinkage/cracking. Improved flexural strength. Density Typical test results Reduces permeability. Better impact/abrasion resistance against site traffic. Improved performance for thinner, bonded screeds where normal minimum thicknesses cannot be achieved. Tarmac SBR Polymer Screed is also available as a selection of traditional prescribed screed mixes. Performance Results based on prisms made, cured and tested in accordance with the requirements of BS EN 13892-2. Tarmac traditional prescribed screed, Results based on cubes, made, cured and tested in accordance with in-house standard operating procedures Product conformity Use in accordance with the recommendations in Code of Practice BS 8204. Tarmac ready-to-use cement sand factory produced screed materials conform to the requirements of BS EN 13813. Tarmac SBR Polymer Levelling Screed should be used in accordance with the recommendations of Codes of Practice BS 8000:Part 9 and BS 8204:Part 1. Compressive strength class Flexural strength class Flexural strength N/mm2 Table 1 – Screed material strength classes. These results are indicative and may be subject to change.
Open the catalog to page 1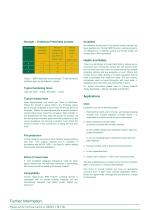
Strength – Traditional Prescribed screeds Designation No problems should occur if the correct screed material has been specified, but Tarmac SBR Polymer Levelling Screed is not designed as a wearing surface and should always be covered with a flooring material. Table 2 – SBR Prescribed screed strength. These results are indicative and may be subject to change. Typical hardening times Health and Safety There is a real danger of contact dermatitis or serious burns. To prevent skin coming into contact with wet cement mixes such as fresh concrete, mortar or screed ensure that suitable...
Open the catalog to page 2
Coverage Area Coverage Area A levelling screed that is laid on a compressible layer such as thermal or sound insulating material should be at least 65mm thick or, if containing heating pipes a minimum of 75mm thick. All conduits should be firmly fixed covered with suitable crack control mesh and given a minimum cover of 25mm. BS 8204-1 recommends that where possible pipes and conduits should not be laid within the thickness of a levelling screed. Floating screed (Minimum thickness 75mm/65mm for light loading) Table 3 – Approximate coverage of screed material NOTE: Slight variations in...
Open the catalog to page 4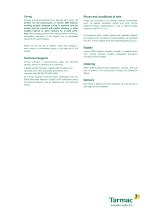
Prices and conditions of sale Screeds should be protected from damage after laying. To achieve the full performance of Tarmac SBR Polymer levelling screeds adequate curing is essential and the screed must be covered with plastic sheeting or other suitable material to retain moisture for at least seven days. Whilst damping down of the surface before covering is acceptable, saturation of the screed, e.g. by prolonged hosing is not recommended. Prices vary according to mix design, quantity and delivery point. For specific quotations contact your local Tarmac Building Products representative or...
Open the catalog to page 5
REFERENCES British Standards Institute BS EN 197-1 Cement Part 1: Composition, specifications and conformity criteria for common cements Specification for limestone fines for use with Portland cement Mixing water for concrete – specification for sampling, testing and assessing the suitability of water, including water recovered from processes in the concrete industry, as mixing water for concrete Admixtures for concrete, mortar and grout: Part 2: 2001 Concrete admixtures – definitions, requirements, conformity, marking and labelling Part 3: 2003 Admixtures for masonry mortar – definitions,...
Open the catalog to page 6All Tarmac Building Products catalogs and technical brochures
-
Topcrete
15 Pages
-
Hemelite
15 Pages
-
Durox
17 Pages
-
Toplite
14 Pages
-
Truflow Datasheet
5 Pages
-
Coloured Mortar Brochure
6 Pages
-
Topblock Sitework Guide
28 Pages
-
Topblock design guide
56 Pages
-
Hemelite and Topcrete
28 Pages
-
Toplite aircrete blocks
16 Pages
-
Durox aircrete blocks
32 Pages
-
Thin joint blockwork
31 Pages
Archived catalogs
-
Tarmac Building
12 Pages