

Catalog excerpts
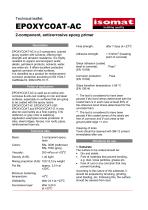
Technical leaflet Description EPOXYCOAT-AC is a 2-component, colored epoxy system with solvents, offering high strength and abrasion resistance. It is highly resistant to organic and anorganic acids, alkalis, petroleum products, solvents, water, sea water etc. It offers excellent protection against corrosion of metal surfaces. It is classified as a product for reinforcement corrosion protection according to EN 1504-7. Certificate Nr. 2032-CPD-10.11. EPOXYCOAT-AC is used as an active anticorrosive & anti-rust coating on iron and steel surfaces, especially on surfaces that are going to be coated with the epoxy resins EPOXYCOAT-W, EPOXYCOAT-VSF, EPOXYCOAT and EPOXYCOAT-S. It may also be used solely as a final coating, if its redbrown or grey color is satisfying. Application examples include protection of silos, steel bridges, fences, iron roofs, pipes, reinforcement bars etc. Basis: Colors: Viscosity: Density (A+B): Mixing proportion (A:B): Pot life: Minimum hardening temperature: Walkability: Successive layer: Final strength: after 7 days at +230C Adhesive strength: > 3 N/mm2 (breaking point of concrete) Shear adhesion (coated steel to concrete): Pass*1 Glass transition temperature: > 68 °C (EN 12614) *1: The test is considered to have been passed if the bond stress determined with the coated bars is in each case at least 80% of the reference bond stress determined for the uncoated bars. *2: The test is considered to have been passed if the coated zones of the steels are free of corrosion and if rust creep at the ground plate edge <1 mm. Cleaning of tools: Tools should be cleaned with SM-12 solvent immediately after use. 1. Substrate The surface to be coated should be: • Dry and stable. • Free of materials that prevent bonding, e.g. dust, loose particles, grease etc. • Free of rust or any corrosion that may prevent bonding. According to the nature of the substrate, it should be prepared by brushing, grinding, sand blasting, etc. Following this, the surface should be cleaned from dust.
Open the catalog to page 1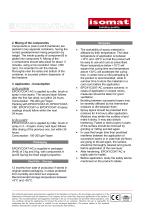
2. Mixing of the components Components A (resin) and B (hardener) are packed in two separate containers, having the correct predetermined mixing proportion by weight. The whole quantity of component B is added into component A. Mixing of the 2 components should take place for about 5 minutes, using a low revolution mixer (300 rpm). It is important to stir the mixture thoroughly near the sides and bottom of the container, to succeed uniform dispersion of the hardener. 3. Application - Consumption a) As a primer EPOXYCOAT-AC is applied by roller, brush or spray in two layers. The second layer...
Open the catalog to page 2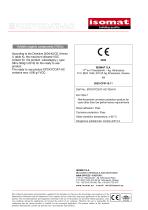
Volatile organic compounds (VOCs) According to the Directive 2004/42/CE (Annex II, table A), the maximum allowed VOC content for the product subcategory j, type SB is 500g/l (2010) for the ready to use product. The ready to use product EPOXYCOAT-AC contains max <500 g/l VOC. C€ 2032 ISOMAT S.A. 17th km Thessaloniki - Ag. Athanasios P.O. BOX 1043, 570 03 Ag Athanasios, Greece 10 2032-CPR-10.11 DoP No.: EPOXYCOAT-AC/1834-01 EN 1504-7 Reinforcement corrosion protection product for uses other than low performance requirements Shear adhesion: Pass Corrosion protection: Pass Glass transition...
Open the catalog to page 3All ISOMAT S.A. catalogs and technical brochures
-
FIBERGLASS FLEECE GF 50 TR
1 Pages
-
ISOMAT AK-60 PU
2 Pages
-
ACCELERATOR 5000
2 Pages
-
MICROCEMENT COATINGS BROCHURE
32 Pages
-
ISOMAT PU-SYSTEMS BROCHURE
20 Pages
-
ISOFLEX-PU 650 BROCHURE
8 Pages
-
Technical Datasheet VS-W
1 Pages
-
Technical Datasheet SM-16
1 Pages