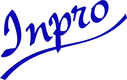
Catalog excerpts
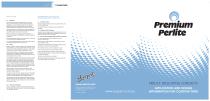
RECOMMENDED PRACTICES FOR WORKMANSHIP AND TOLERANCES 6.1 – Placement Perlite concrete should be conveyed from the mixer to the place of final deposit by methods which will prevent segregation or loss of material. Equipment for conveying perlite concrete should be designed to ensure delivery without separation of materials or serous loss of air content. Pumping should be in accordance with recommendations of the perlite producer, and the perlite concrete shall meet the specified properties at the point of placement. Perlite concrete should be deposited and screeded in a continuous operation until the placing of a panel or section is completed. 7.1 – Variation of Plane Variation in deck thickness should be no greater than 6.5 mm on a 3m straight edge. This tolerance does not include variations resulting from substrate. 7.2 – Variation in Deck Thickness Variation in deck thickness should be no greater than 6.5 mm from specified thickness established by averaging measurements taken at 3 points on a 3m x 3m square. 7.3 – Rain or Freezing Damage Before Setting of Concrete Expanded polystyrene board should be placed in a minimum 3.1 mm wet slurry of insulating concrete. It is recommended the deck be allowed to cure for a minimum of three days. It is recommended the board be covered by perlite concrete to finished thickness before the slurry is set. After freezing or heavy rainfall give a thorough brooming if required before roofing. That portion of the deck which has excessive sealing should be removed to solid concrete, and patched. Normal Conditions: Perlite concrete has an adequate mixing water content so as to have sufficient water for proper curing of the concrete without additional precautions. Under these conditions the concrete should be permitted to air dry. Path additives may be used at the applicator’s option. If minor scaling occurs broom surface before roofing. Extreme Dry Conditions: When perlite concrete is placed during extreme dry weather, additional water may have to be sprinkled on the concrete for a sufficient period of time to allow hydration of the concrete. Perlite concrete exposed to extreme cold after setting will provide adequate strength to receive roofing if not subjected to mechanical damage. Cold Weather Conditions: For winter pouring the use of high early strength (Type III) Portland cement is recommended. All concrete materials, reinforcement and forms with which the perlite concrete may come in contact should be free of frost. No frozen material or materials containing ice should be used. When it is anticipated outside temperature will be below 4oC. 24 hours after placing of the concrete, the mixing water should be heated to a maximum of 48oC. Damage after placement caused by other trades should not be the responsibility of the applicator. Therefore, all traffic should be prohibited. Perlite insulating concrete should not be placed during freezing weather unless the contractor is experienced in the special techniques required. The built-up roofing should be applied as soon as the perlite insulating concrete can carry construction traffic, and is dry enough to develop adhesion with hot asphalt or pitch. Roof application should proceed when the perlite concrete has been cured a minimum of three days. Provision shall be made for perimeter or edge venting by use of an open metal gravel guard or facia. PERLITE INSULATING CONCRETE 6.3.1 – Mechanical Fasteners Nailing or stapling are preferred methods of attachment for the base sheet, and shall be used on perlite concrete applied over structural concrete. APPLICATION AND DESIGN INFORMATION FOR CONTRACTORS
Open the catalog to page 1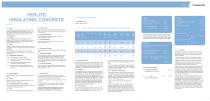
PERLITE INSULATING CONCRETE Shall be a highly compressible vapour permeable material which will compress to one half its thickness under a load of 172 kPa or less. Perlite insulating concrete is a combination of perlite aggregate, Portland cement, air entraining agent, water and/ or other additives producing a concrete with an oven dry density of 800 kg/m3 or less. 2.6 – Embedded Insulation Shall be expanded polystyrene insulation board with a minimum density of 16 kg/m3. Net weight of water: Volume = Net Weight of water _________________ Density of water: TYPICAL PHYSICAL PROPERTIES OF...
Open the catalog to page 2All Inpro catalogs and technical brochures
-
Perlite Concrete
2 Pages
-
Premium Perlite
6 Pages
-
The Perlite House
1 Pages