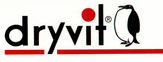

Catalog excerpts
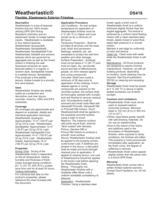
Weatherlastic® DS418 Flexible, Elastomeric Exterior Finishes Description Weatherlastic is a line of textured finishes that are 100% acrylic, utilizing DPR (Dirt Pickup Resistant) chemistry and an elastomeric binder to bridge hairline cracks. Weatherlastic is available in four distinct textures. Weatherlastic Quarzputz®, Weatherlastic Sandpebble®, Weatherlastic Sandpebble® Fine, Weatherlastic Adobe® and achieve textures which are governed by aggregate size as well as the trowel motion in finishing the wall. Quarzputz produces an opentextured pattern in a regular or random style, Sandpebble trowels to a pebble texture, Sandpebble Fine produces a fine pebble texture; Adobe trowels to a smooth, fine sand texture. Uses Weatherlastic finishes are ideally suited as a protective and decorative coat over stucco, concrete, masonry, CMU and EIFS substrates. Coverage All coverages are approximate and depend on substrate, details and individual application technique. Weatherlastic Quarzputz: Approximately: 13 m2 (140 ft2) per 32 kg (70 lb.) pail. Weatherlastic Sandpebble: Approximately 12 m2 (130 ft2) per 32 kg (70 lb.) pail. Weatherlastic Sandpebble Fine: Approximately 14 m2 (150 ft2) per 32 kg (70 lb.) pail. Weatherlastic Adobe: Approximately 18 m2 (190 ft2) per 32 kg (70 lb.) pail. Properties Drying Time - Drying of the Weatherlastic finish is dependent on the air temperature, relative humidity and thickness of finish. Under average drying conditions [21 °C (70 °F), 55% R.H.], protect work from rain for at least 24 hours. Testing Information: For individual test data on this product’s properties, please reference the chart included with this document. Application Procedure Job Conditions - Air and surface temperature for application of Weatherlastic finishes must be 4 °C (40 °F) or higher and must remain so for a minimum of 48 hours. Temporary Protection - Shall be provided at all times until the base coat, finish and permanent flashings, sealants, etc. are completed to protect the wall from weather and other damage. Surface Preparation - Surfaces must not be below 4 °C (40 °F) and must be clean, dry, structurally sound and free of efflorescence, grease, oil, form release agents and curing compounds. Concrete: Shall have cured a minimum of 28 days prior to application of the coatings. If form release agents or curing compounds are present on the concrete surface, the surface shall be thoroughly washed with muriatic acid and flushed to remove residual acid. All projections shall be removed and small voids filled with Genesis® Primus®, Genesis® DM or Primus® DM mixture. Dryvit Weatherprime® shall be applied to the prepared concrete surface using a roller or brush. Masonry: The masonry surface, with joints struck flush, shall be "skim coated" with Genesis, Primus, Genesis DM or Primus DM mixture to produce a smooth, level surface. Stucco: Weatherlastic finishes shall be applied to the properly primed, cured brown coat. If additives are present in the stucco, a test patch shall be made and bond strength checked prior to application. If applied to existing stucco, one coat of Weatherprime should be applied to the brown coat before applying the Weatherlastic finish. Mixing - Thoroughly mix Weatherlastic finishes with a Goldblatt Jiffler Mixer until a uniform workable consistency is attained. Application - Weatherlastic Finishes: Using a stainless steel trowel, apply a level coat of Weatherlastic finish to a uniform thickness slightly thicker than the largest aggregate. The texture is achieved by a uniform hand floating motion with a clean stainless steel trowel, plastic trowel or wood float. Apply light pressure in a circular motion. Maintain a wet edge for uniformity of color and texture. Clean Up - Clean tools with water while the Weatherlastic finish is still wet. Maintenance - All Dryvit products are designed to require minimal maintenance. However, as with all building products, depending on location, some cleaning may be required. See Dryvit publication DS152 on cleaning and recoating. Storage Weatherlastic finish must be stored at 4 °C (40 °F) or above in tightly sealed containers out of direct sunlight. Cautions and Limitations • Weatherlastic finish must not be used on exposed exterior horizontal surfaces. Minimum slope is 152 mm (6 in) in 305 mm (12 in) (27°). • When used below grade, backfill with well-draining materials. Do not use as waterproofing. • Due to the nature of the resins and additives used in the formulation of Weatherlastic finishes, when exposed to damp conditions, the finishes will soften. This property is more pronounced immediately after application; as the finish cures, the degree of softening is reduced. • Weatherlastic finish colors appear slightly darker than the same color in a Dryvit DPR finish. Warranty Weatherlastic finish comes with a written limited material warranty. Contact Dryvit Systems, Inc. for full details.
Open the catalog to page 1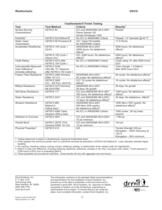
Weatherlastic DS418 Weatherlastic® Finish Testing Criteria Test Test Method Surface Burning Characteristics ASTM E 84 Flexibility2 Water Vapor Transmission Accelerated Weathering ASTM D 522 Method B ASTM E 96 Procedure B ASTM G 154 Cycle 1 (QUV) Salt Spray Resistance ASTM G 155 Cycle 1 (Xenon Arc) ASTM D 4214 after ASTM G 154 Cycle 1 ASTM D 2244 CIELAB, 10° Observer after ASTM G 154 Cycle 1 ASTM E 2485 (formerly EIMA 101.01) ASTM E 2485 ICC – ES Proc. (AC212) ASTM D 3273 (formerly Mil Std-810B) ASTM B 117 Water Resistance ASTM D 2247 Abrasion Resistance ASTM D 968 Method A Falling Sand ASTM...
Open the catalog to page 2All Dryvit catalogs and technical brochures
-
Weatherlastic ® Smooth
2 Pages
-
Dryvit Systems
1 Pages
-
Tuscan Glaze
6 Pages
-
TerraNeo®
6 Pages
-
Cement Board MD Finish System™
20 Pages
-
Outsulation® Plus MD System
26 Pages
-
DS199
15 Pages
-
Outsulation MD System®
24 Pages
-
DS171
31 Pages
-
Infinity® System
28 Pages
-
DS113
22 Pages
-
DryvitCARE
33 Pages
-
cUSTOM BRICKS
2 Pages